In today’s world, countless industries rely on machinery and equipment to perform tasks efficiently and productively. While these tools undeniably contribute to progress, their inherent power necessitates a crucial element: safety.
This article emphasizes the importance of comprehensive employee training as the cornerstone of safe equipment operation. By equipping workers with the necessary knowledge, skills, and awareness of potential risks, we can foster a work environment where productivity and safety go hand in hand.
The Necessity of Equipment Training
Operating machinery without proper training is akin to navigating unfamiliar territory blindfolded – the risks are significant and the consequences potentially devastating. Comprehensive equipment training equips employees with the following crucial elements:
- Correct Usage: Training delves into the intended purpose, functionalities, and limitations of specific equipment. This empowers workers to operate the machinery effectively and efficiently, avoiding misuse and potential damage. For example, a forklift operator should understand the weight capacity of the machine, safe lifting techniques, and proper maneuvering procedures to prevent overloading, tip-overs, and collisions.
- Safety Protocols: Understanding established safety procedures is paramount. Training covers areas like:
- Personal protective equipment (PPE) requirements: This includes understanding the various types of PPE needed for specific tasks and how to wear and maintain them properly. For example, construction workers might require hard hats, safety glasses, gloves, and steel-toed boots depending on the equipment and tasks involved.
- Lockout/tagout procedures: These procedures ensure that energy sources are isolated and secured before maintenance or repairs are performed, preventing accidental startup and potential injuries.
- Emergency response protocols: Training equips workers to respond effectively in case of emergencies, such as equipment malfunctions, fires, or spills. This includes knowing how to use emergency equipment, evacuate safely, and report incidents.
- Hazard identification and mitigation strategies: Training empowers workers to identify potential hazards associated with equipment operation, such as pinch points, sharp edges, electrical hazards, and falling objects. Additionally, it teaches them mitigation strategies like maintaining safe distances, using proper lifting techniques, and following established safety procedures to minimize the risk of injury.
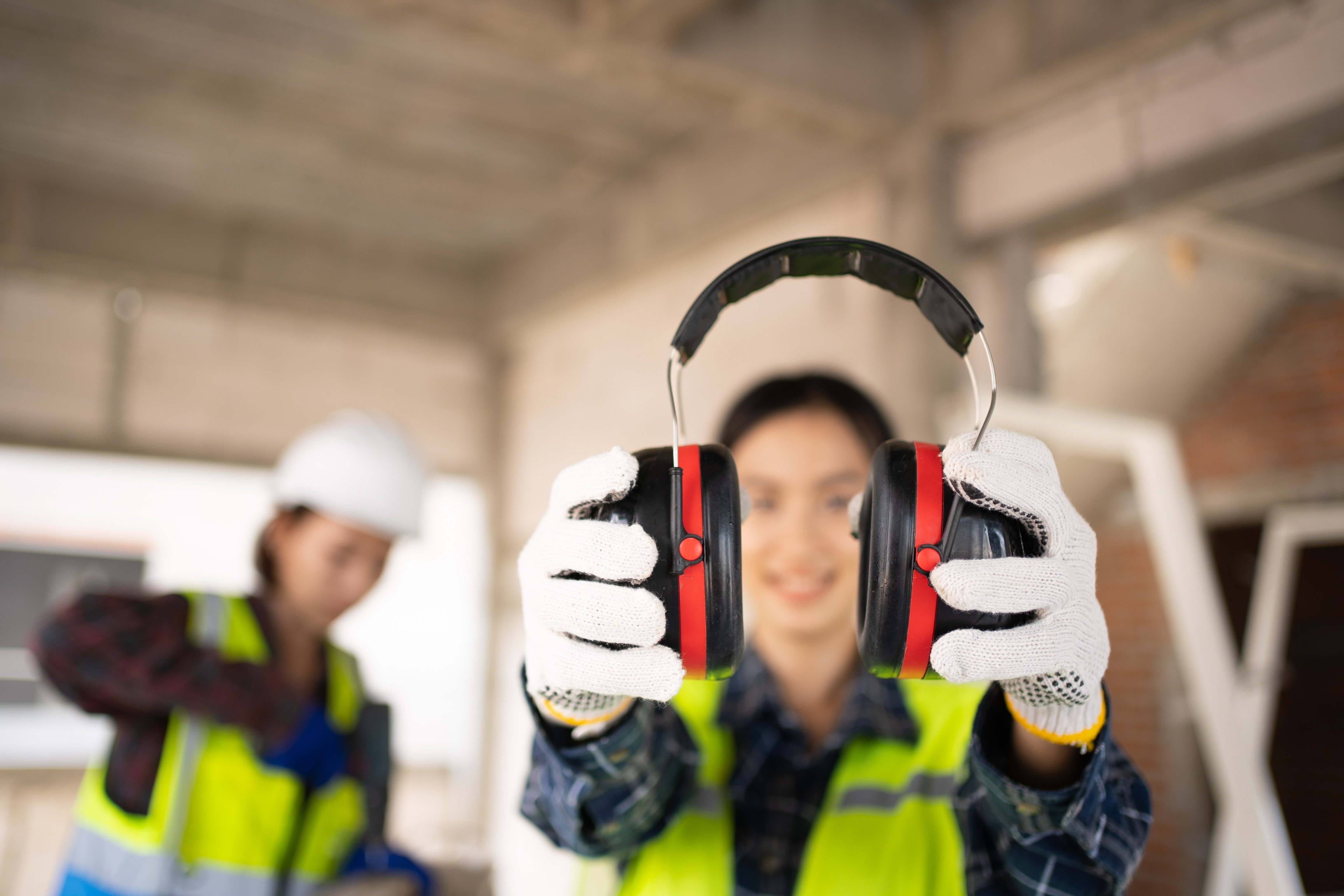
- Risk Awareness: Training fosters a culture of risk awareness by highlighting the potential dangers associated with improper equipment use. This empowers employees to:
- Recognize and avoid hazardous situations: By understanding the risks involved, workers can be more proactive in identifying potential dangers and taking steps to avoid them. This could involve refusing to operate malfunctioning equipment, reporting unsafe work conditions, and following established safety protocols even when under pressure.
- Develop a safety-conscious mindset: Effective training instills a safety-first mentality in employees, encouraging them to prioritize their own safety and the safety of their colleagues. This fosters a collaborative environment where everyone plays a role in maintaining a safe work environment.
By equipping employees with this comprehensive knowledge base, equipment training empowers them to operate machinery with confidence, competence, and a strong understanding of the potential consequences of their actions. This not only safeguards their well-being but also contributes to a safer and more productive work environment for everyone.
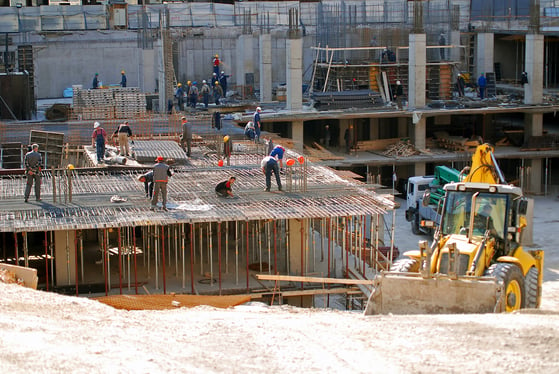
Benefits of Effective Equipment Training
Investing in effective equipment training transcends legal requirements; it yields a multitude of benefits for both employers and employees:
- Reduced Accidents and Injuries: Properly trained employees are less likely to make mistakes that could lead to accidents or injuries. This translates to:
- Fewer worker injuries and illnesses: This not only protects the physical and mental well-being of employees but also minimizes the emotional and financial toll of workplace incidents on individuals and families.
- Lower workers’ compensation costs: Fewer accidents and injuries lead to a decrease in workers’ compensation claims, saving organizations significant financial resources.
- Reduced downtime: When accidents occur, it disrupts operations and can lead to production delays and lost productivity. Effective training helps minimize downtime by preventing incidents and ensuring a smooth workflow.
- Improved Productivity: When employees feel confident and competent in operating equipment, they can work more efficiently and productively. This translates to:
- Increased output: Employees who understand how to use equipment effectively can complete tasks more quickly and accurately, leading to higher production levels.
- Reduced waste and rework: Proper training can help minimize errors and ensure tasks are completed correctly the first time, reducing the need for rework and saving time and resources.
- Improved overall efficiency: A well-trained workforce can streamline operations, optimize resource allocation, and contribute to a more efficient work environment.
- Enhanced Morale: A strong focus on safety demonstrates an employer’s commitment to protecting its workforce. This translates to:
- Increased employee trust and confidence: When employees feel valued and their safety is prioritized, they are more likely to be engaged, motivated, and loyal to their organization.
- Improved employee morale: A safe and supportive work environment fosters a sense of well-being and job satisfaction, leading to higher morale and a more positive workplace culture.
- Reduced employee turnover: When employees feel valued and safe, they are less likely to seek employment elsewhere, contributing to lower turnover rates and associated costs.
- Reduced Costs: Beyond the direct costs of accidents and injuries, various other financial benefits stem from effective training:
- Lower insurance premiums: Organizations with a strong safety record may qualify for lower insurance premiums on workers’ compensation and other liability insurance policies.
- Reduced legal expenses: Effective training can help mitigate the risk of lawsuits arising from workplace accidents and injuries, minimizing potential legal costs.
- Improved brand reputation: A commitment to safety can enhance an organization’s brand reputation and attract top talent, contributing to long-term success.
Beyond the Basics: Continuous Learning and Improvement
Effective equipment training is not a one-time event; it’s an ongoing process that requires continuous learning and improvement to maintain a safe and productive work environment. Here are some key aspects to consider:
- Regular Refresher Courses: Technology advancements, changing regulations, and evolving best practices necessitate periodic refresher courses. These sessions help employees stay up-to-date on the latest equipment operation procedures, safety protocols, and hazard identification strategies. Refresher courses can be tailored to specific equipment or address newly identified risks.
- Promoting a Learning Culture: Fostering a culture of continuous learning within the organization encourages employees to take ownership of their safety and actively seek opportunities to improve their knowledge and skills. This can be achieved through:
- Encouraging open communication: Employees should feel comfortable asking questions, reporting near misses, and suggesting safety improvements without fear of reprisal.
- Providing access to resources: Organizations can offer resources like safety manuals, online training modules, and access to safety professionals to empower employees to continually learn and stay informed.
- Encouraging peer-to-peer learning: Experienced employees can share their knowledge and best practices with newer colleagues, fostering a collaborative learning environment.
- Adapting to Change: The workplace is constantly evolving, and equipment updates and technological advancements are inevitable. Adapting training programs to reflect these changes is crucial. This might involve incorporating new equipment operation procedures, addressing safety considerations for emerging technologies, and ensuring training materials stay current and relevant.
- Data-Driven Decision-Making: Organizations can leverage data from incident reports, near misses, and safety audits to identify areas for improvement in their training programs. This data-driven approach can help tailor training to address specific needs and ensure its effectiveness in mitigating risks and preventing incidents.
By implementing these practices, organizations can move beyond the basic training requirements and establish a sustainable approach to safety and continuous improvement. This commitment to ongoing learning empowers employees to remain competent, adaptable, and safety-conscious, contributing to a thriving work environment where productivity and safety are not mutually exclusive, but rather, complementary elements of success.
Mastering the Machine: A Journey of Continuous Learning and Shared Responsibility
In today’s world, machinery and equipment are the driving forces behind countless industries, propelling progress and innovation. However, with this power comes an inherent responsibility – the responsibility to prioritize safety and ensure that every interaction with equipment is conducted with knowledge, awareness, and a commitment to mitigating risks.
This article has emphasized the crucial role of comprehensive employee training in safeguarding the well-being of workers and fostering a productive work environment. By equipping individuals with the necessary skills, knowledge, and risk awareness, we empower them to operate machinery with confidence and competence.
However, effective equipment safety extends beyond the initial training session. It necessitates a commitment to continuous learning and improvement. This ongoing journey involves:
- Regularly refreshing and adapting training programs to stay abreast of evolving technologies, changing regulations, and emerging safety considerations.
- Fostering a culture of open communication and peer-to-peer learning where employees feel empowered to ask questions, share best practices, and report near misses without fear of reprisal.
- Leveraging data-driven insights from incident reports, near misses, and safety audits to identify areas for improvement and tailor training programs to address specific needs.
By embracing this comprehensive approach, organizations and employees alike can embark on a shared journey toward mastering the machine. This journey fosters a safety-conscious mindset, where individuals prioritize their well-being and the safety of their colleagues. It cultivates a collaborative environment where continuous learning and improvement are encouraged, and where productivity and safety are not competing priorities, but rather, complementary elements that pave the way for a successful and sustainable future.
Remember, safety is not a destination; it’s an ongoing journey. By prioritizing continuous learning, collaboration, and a shared commitment to safe practices, we can ensure that every interaction with machinery empowers individuals, safeguards well-being, and paves the way for a brighter and safer future for all.
