When safety fails, the consequences aren’t just regulatory, they’re human. That’s why the best EHS leaders don’t just rely on gut instinct. They rely on data.
Tracking the right EHS key performance indicators (KPIs) helps organizations reduce injuries and stay OSHA compliant. But with so many metrics available, which ones truly matter?
This guide breaks down the most critical EHS KPIs, what they measure, why they matter, and how to track them in a way that drives action and accountability.
What Are EHS KPIs?
What is an EHS KPI? It’s a metric used by safety teams to measure compliance, injury rates, and overall workplace risk. They’re more than just reports, they guide action. When tracked correctly, these indicators give safety leaders a clear view of progress, gaps, and emerging risks across jobsites and departments.
There are two categories that matter most:
Lagging Indicators Reflect Past Events: Lagging indicators include things like injury rates, lost workdays, or recordable incidents. These metrics help teams understand the impact of past performance and assess whether safety efforts have successfully reduced harm over time.
Leading Indicators Highlight Future Risk: Leading indicators can include near miss reports, overdue training, or missed inspections. They are essential to proactive safety because they help teams identify and address issues before someone gets hurt.
Now that the key types of KPIs are clear, let’s look at why they’re so widely used by safety leaders.
Why Safety Leaders Rely on KPIs
Why do safety leaders rely on EHS KPIs? Because they turn safety goals into clear, trackable actions. Here’s how KPIs bring structure, clarity, and results.
- Provide Visibility to Leadership: Most executives aren’t reading safety manuals; they want numbers. KPIs turn safety data into clear, trackable numbers that leadership understands.
- Focus Resources Where They’re Needed: Not every jobsite faces the same hazards. If one location shows a spike in near misses or a drop in training completions, it signals where to act. KPIs help leaders prioritize site visits, retraining, or equipment upgrades with data, not guesswork.
- Build Accountability Across Teams: When everyone knows what’s being tracked and why, they’re more likely to follow through. KPIs help convert broad safety goals into daily expectations. Whether it’s completing inspections or closing corrective actions, metrics keep teams aligned and accountable.
But those benefits only come when you’re tracking the right things. Not every metric adds value, and some can even distract.
Top EHS KPIs for Organizations
The best EHS KPIs are simple to measure, tied to real-world risk, and easy to act on. These are the ones safety leaders trust to spot problems early, stay compliant, and protect their teams.
1. Total Recordable Incident Rate (TRIR):
TRIR provides a standardized way to measure injury frequency across different job sites, departments, or contractors. A high TRIR can raise red flags during third-party audits or corporate reviews. A low TRIR can help maintain contract eligibility and boost reputation.
Many safety managers set internal TRIR thresholds to trigger follow-up investigations or extra training. Insurance providers also use TRIR when setting premiums. In the construction industry, companies with a TRIR above the national average may be disqualified from bidding on federal projects.
2. Days Away, Restricted, or Transferred (DART):
DART doesn’t just track injuries, it focuses on injuries that disrupt work. These are the cases most likely to affect productivity and long-term workforce health. DART is a strong indicator of how well an organization prevents serious harm.
OSHA uses DART as part of its Site-Specific Targeting (SST) program, which identifies high-risk employers for inspection. A rising DART score may also trigger internal reviews or retraining in high-hazard roles.
3. Near Miss Reporting Rate:
This KPI reflects culture as much as performance. High near miss reporting means your team is trained to recognize hazards and feels safe reporting them. It’s one of the few ways to measure invisible risk and your company’s safety culture.
Near miss data can uncover unsafe equipment, poor ergonomics, or risky behavior before someone gets hurt. Safety leaders often set monthly near miss targets to encourage engagement.
4. Corrective Action Completion Rate:
Finding a hazard isn’t enough, it needs to be resolved. This KPI helps ensure safety issues don’t linger. Inconsistent closure rates may signal breakdowns in accountability or communication.
Some organizations use thresholds, like “90% of corrective actions closed within 30 days”, as a performance target. This KPI also helps prepare for OSHA audits, where inspectors may ask to see how long open items remain unresolved.
5. Safety Training Completion Rate:
Incomplete training records are a compliance risk. More importantly, they increase the chance that someone gets hurt because they didn’t know the proper procedure. This KPI reflects both compliance and readiness.
During an OSHA inspection, a compliance officer may ask to see evidence of training for lockout/tagout, respiratory protection, or hazard communication. Real-time tracking ensures that all required topics are covered and no one is left behind.
Tracking these metrics is essential, but how you track them can make or break your program.
Best Practices for Tracking EHS KPIs
High-performing EHS teams follow a set of habits that keep their metrics reliable and decision-ready.
1. Stick to OSHA Definitions
Mislabeling a recordable injury or misclassifying a restricted duty case can lead to underreporting or even penalties. Teams that stick to the language and definitions remove confusion, especially when multiple sites or contractors are involved.
2. Centralize Your Data
Scattered spreadsheets and siloed systems create blind spots. When data lives in multiple places, one system for incidents, another for training, and a third for inspections, it’s nearly impossible to get a full picture. A centralized dashboard, even a simple one, allows teams to compare performance across jobsites and spot risks faster.
3. Automate Wherever Possible
Manual reporting eats up time and often introduces human error. When corrective actions are closed out in notebooks or emails, it’s easy for things to slip through the cracks. Automated systems ensure that audits trigger follow-up actions, overdue training sends reminders, and near misses get logged in real time.
4. Review Consistently
Set a review rhythm that matches your risk. Some teams meet monthly, others review KPIs quarterly. The timing matters less than the consistency. Regular reviews also make it easier to adjust when trends shift, rather than reacting after something goes wrong.
Still, even well-planned systems can run into trouble.
Mistakes and Challenges When Tracking EHS KPIs
Avoiding these common pitfalls can make the difference between useful data and numbers that lead nowhere.
1. Relying on Spreadsheets
It’s tempting to use what’s familiar, but spreadsheets weren’t built for dynamic tracking. If multiple people update the same file, or if someone copies data from the wrong version, your metrics lose reliability. Version control problems and formula errors can seriously mislead leadership.
2. Inconsistent KPI Definitions
Inconsistent definitions make it hard to set corporate goals or explain results to executives. This often happens when onboarding new sites or switching reporting platforms. Setting and communicating clear, company-wide definitions is a must.
3. Ignoring Near Miss Trends
A rise in near misses is often the first clue that a serious injury could happen soon. If near miss reports are filed but never reviewed, opportunities for prevention are lost. The best teams treat near misses as a gold mine of learning. They don’t just track how many are reported, they also look for patterns: Are they happening on the night shift? Near loading docks? During maintenance?
4. No Real-Time Visibility
If you have to wait until the end of the quarter to know what’s going on, it’s already too late. Real-time dashboards help managers intervene early, whether it’s rerunning training, rechecking PPE, or adding a guard to a machine. Without this, you’re flying blind between reports, and that’s when small risks become major incidents.
Avoiding these mistakes sets a strong foundation. The next step is using tools that make tracking easier, faster, and more reliable.
How EHS Insight Helps Safety Leaders Track KPIs
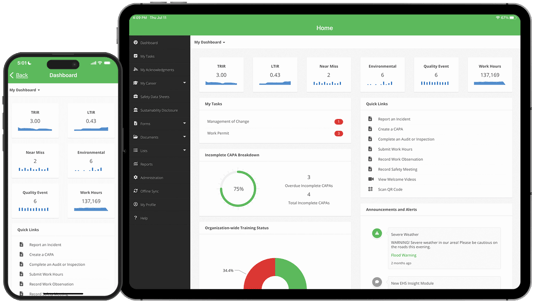
EHS Insight was designed to take the guesswork out of safety management and tracking. It gives safety leaders the tools they need to track KPIs with speed, accuracy, and confidence, without getting buried in spreadsheets or manual reports.
- Incident Management: Automatically calculates OSHA-compliant TRIR and DART rates. No more chasing down logs or second-guessing your math.
- Audit and Inspection Tools: Schedule audits, assign corrective actions, and monitor closure rates.
- Training Management: Track completions, expiration dates, and missed sessions. You’ll know exactly who’s trained and who needs a reminder, before an inspector asks.
- Corrective Actions: Assign tasks, set deadlines, and monitor follow-through with built-in workflows. Nothing gets lost, and nothing slips through the cracks.
- Business Intelligence Connector: Get instant visibility with live dashboards and exportable OSHA-ready reports. Spot trends, compare sites, and stay audit-ready.
- AI-Driven Tools: Surface hidden patterns in your data to flag potential high-risk conditions, before they lead to incidents.
Strong safety programs don’t rely on guesswork. They rely on data that’s accurate, visible, and easy to act on. EHS Insight helps you track the metrics that matter, avoid compliance gaps, and build a safer, more accountable workplace. Schedule a demo today and see how our software can help you take control of your KPIs and drive safety forward.
FAQs
What’s the difference between a TRIR and a DART rate?
TRIR measures the total number of recordable incidents per 100 full-time workers, while DART focuses only on cases that led to days away, restricted duties, or job transfers. They tell different stories about injury severity.
How do I calculate TRIR and DART?
Use this formula:
(TRIR) = (Number of Recordable Incidents × 200,000) ÷ Total Hours Worked
(DART) = (Number of DART Cases × 200,000) ÷ Total Hours Worked
Can EHS software generate OSHA 300 and 301 logs?
EHS Insight automatically generates OSHA 300 and 300A logs, along with a 301 summary report and ITA import file for electronic submission.
